"DL E&C Easily Manages Risks for Sites That Have Adopted Meissa."
"Construction Sites Are Complex With Various Partners and Processes, and Dozens of Workers Participate in Work on a Daily Basis. Recording Every Moment of the Situation Without Losing Sight of It Is the Core of Project Management. In Particular, the Importance of Accurate and Timely Field Records Is Emphasized to Prevent and Resolve Problems That May Arise During Cooperation With Multiple External Companies and Stakeholders.
In This Context, DL E&C Introduced Meissa. This Goes Beyond Simply Collecting Data; It Aims to Integrate All Relevant Information to Maintain a Consistent Work Environment and Data Flow. This Integrated Approach Maximizes the Efficiency of Construction Projects and Enables Decision-Making Based on Clear and Reliable Information at Each Stage.
Challenge :
Low On-Site adoption rate for New Technologies
Q. Please Give Us a Brief Introduction.
We Are Part of the Convergence Technology Team, and the Team Mainly Deals With Various Technologies Related to Construction. This Includes Smart Construction, Smart Home, and Home Visualization Solutions Using Drones, AI, VR, and Sensor Technologies. The Team's Main Mission Is to Introduce and Rapidly Spread New Technologies to Advance the Construction Industry. Meisㄴa Was Also Introduced for the Same Purpose. The Biggest Challenge Right Now Is to Think About Ways to Make It Easy for People to Accept and Use These New Technologies.
Q. For the Adopted Drone Platform, Why Meissa?
The Core Goal of Introducing the Drone Platform Is to Improve Work Productivity in the Field and Streamline Company-Wide Record Management. By Digitizing and Automating Tasks That Were Previously Performed Manually and Conventionally, Processes, Construction, and Safety Tasks Can Be Made Smarter. A Simple Panoramic Photo Alone Will Not Be of Much Help. It Should Be Possible to Easily Measure the Location, Distance, Area, and Volume of the Site Through Data Including Coordinate Values, and the Difference Between the Drawing and Actual Space Should Be Visible at a Glance by Uploading Accurate Drawings. All of This Management Is Applied Equally to Over 70 Sites.
Before the Introduction of Meissa, an Overseas Platform Was Used for the Same Purpose, and Users Were Initially Surprised but Satisfied. However, as Time Passed, It Became Increasingly Difficult to Meet Field Demands. he Platform Was Limited to Checking On-Site Photos, and Its Usability for Actual Process/Construction/Safety Management Purposes Began to Decline. Naturally, the Frequency of Using the Platform Has Decreased. In That Sense, the Biggest Reason for Choosing Meissa Can Be Said to Be Continuous Customer Support and the Possibility of Future Development.
In Fact, More Than 10 Hours of Earthwork Volume Calculation Required Before the Introduction of Meissa Can Now Be Done in Just 10 Minutes. The Preparation Time for Daily Safety and Process Meetings, Which Used to Take an Hour Each Day, Has Also Disappeared. Substantial Simplification of Work Has Been Achieved, and Satisfaction Levels Are Very High Both in the Field and at Headquarters.
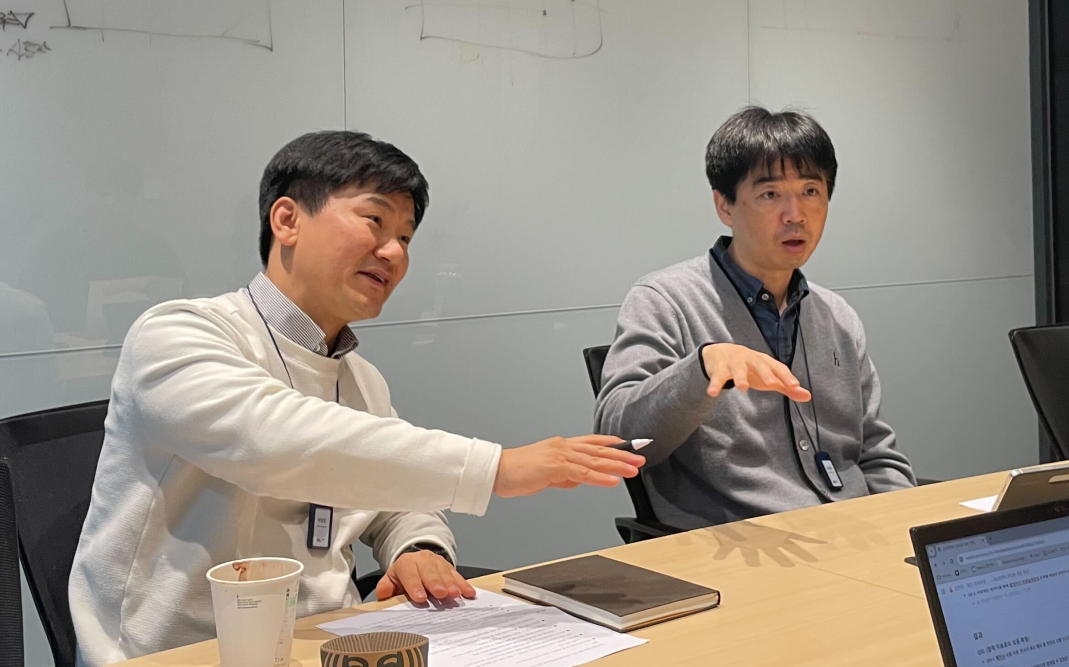
Managing the entire site through one platform
Q. How is Meisa currently used?
Through standardization, it is being applied and utilized in about 70 housing, civil engineering, and plant sites, and this consistent work environment enables communication within the site, communication between the site and headquarters, and communication between the site and headquarters and outsourcing companies. and work efficiency.
Daily safety and fairness meetings (DSPM meetings) are held at our sites every day. Previously, layout plans or individual photos taken with smartphones were displayed on the large screen in the conference room to give work instructions or establish a work plan for the day. It was impossible to give accurate work instructions using drawings that were not actual images, and it was difficult to understand the overall status by only reporting a few photos. This made communication difficult, resulting in rework due to unclear work instructions.
However, through the Meissa drone platform, you can see the outside without blind spots by viewing 2D orthophotos and 3D modeling screens together, and much more accurate and clear work has become possible.
All employees at all sites across the company can make hypotheses with the same field data. Establish plans, check drawing/construction differences, calculate quantities, and make decisions.
Previously, only the total earthwork volume could be calculated for each zone, making it difficult to manage trends by date and by zoning/type, and it was difficult to manage the most important earthwork process in detail in the early stages of construction. However, through the performance management platform compared to the earthwork volume plan, quantity calculation by date/zoning/characteristics, construction management, and settlement management can all be managed at once, making precise earthwork process management possible, and resolution of construction and settlement issues with earthwork companies. It disappeared naturally.
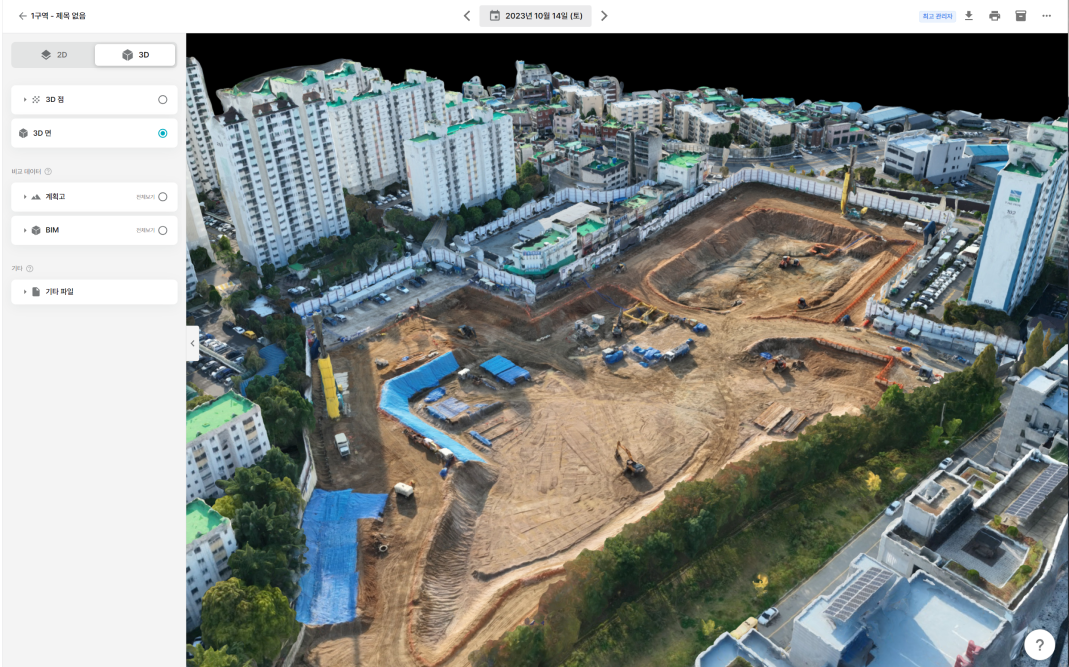
e-Pyeonhansesang Siheung Double Square New Construction Site in Progress
"When a problem arises, only the necessary information is missing!"
Q. So how are the kept records used?
They are used to actively respond to field issues.
No matter how carefully you manage things, there are issues with records in the field. As a joke, “When a problem arises, the only information you need is missing!” There are also cases where it is said. In reality, the distance between headquarters and the field is too far. Therefore, we reduced communication costs between headquarters and sites through a drone platform that allows 3D visual communication. By storing drone data on the platform, sites can improve work productivity and at the same time prevent risks due to missing records.

Zoning area drawing function applied to the field.
To give a clear example of risk prevention, there is Maysa's earthwork performance management platform. At the site, it is difficult to manage and settle the existing quantity compared to ordering by quantity and nature during earthworks, but through the Meisa platform, you can easily manage the final quantity from quantity calculation to established management and settlement. Thanks to this, employee productivity has improved significantly compared to before the introduction, and disputes with partners that occurred every month were eliminated.
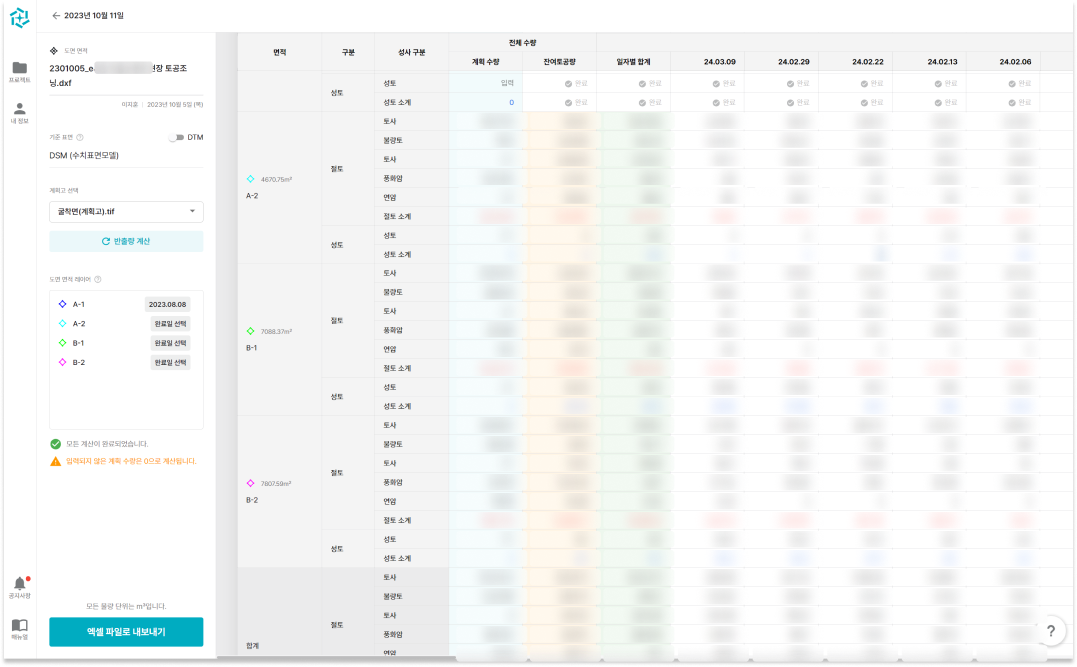
Earthwork tally table function used in Siheung Double Square new construction
DL E&C and Meissa: Smart Construction of the Future Together
Q. What more would you like to do with Meissa in the future?
A construction site drone management solution must go beyond providing 3D digital twin data and develop and provide functions needed in actual sites. An example is the performance management solution for earthwork plans developed and provided with DL E&C and Meissa in 2023.
We plan to continue to pursue cooperation with Meissa in the future. What is planned is to additionally develop quality control and safety management solutions for pile work and frame work, and expand the scope of application to construction work.